ALPINE ADVANCED MATERIALS TAKES AIM AT FIREARMS INDUSTRY WITH HIGHLY MANUFACTURABLE ADVANCED THERMOPLASTIC NANOCOMPOSITE
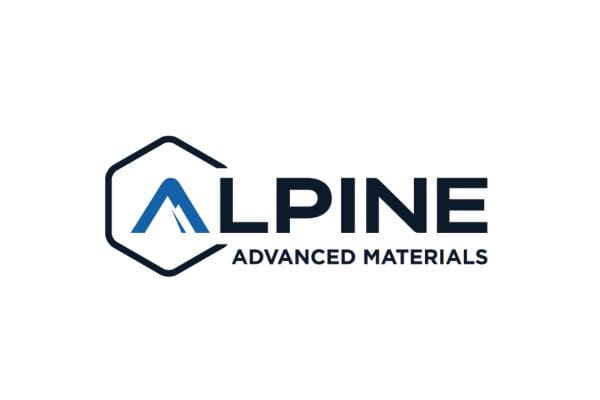
With a Low Thermal Coefficient of Expansion, HX5 is Perfectly Suited for Firearms at Half the Weight and 90% the Strength of 6061-T6 Aluminum
Alpine Advanced Materials is taking aim at the firearms industry with its HX5™ military aviation-grade thermoplastic nanocomposite. A material option that is 50% lighter and 90% the strength of 6061-T6 aluminum, HX5 also boasts a low thermal coefficient of expansion at a sixth that of 6061-T6, making it ideal for use in components like stocks, rails, mounts, grips, and sights.
Stronger than traditionally injection-molded thermoplastics, HX5 is ideal to replace metals where extreme endurance, weight, and performance matter, especially for thin or complex parts. Firearms are exposed to both internal and external temperature fluctuations, but materials like aluminum and steel can cause parts to expand or contract more than a material with a low coefficient of thermal expansion. Also, while one surface is exposed to extreme heat, the opposite may be exposed to cold or need to remain cool, making a material’s temperature tolerance of even greater import.
“Firearms need to work correctly the first time, every time, but their usability can be compromised if a critical feature has moved due to temperature,” said Roger Raley, president of Alpine Advanced Materials. “With a sixth of the thermal coefficient of expansion of aluminum, HX5 gives a higher chance that components and safety features will more likely be positioned correctly within any operating environment. This is key for manufacturers that want to instill as much confidence in both their product and brand.”
Engineered to replace machined aerospace-grade aluminum at half the weight, HX5 has both a high tensile and compressive strength, low thermal conductivity, and is non-abrasive. It is also extremely corrosion-resistant, with no cosmetic or performance degradation after exposure to UV, DEET, or various fuels and solvents. Tested against the harshest environments on earth, it has demonstrated resistance to temperatures as high as 500°F and as low as -65°F. HX5 also coats well for both functional and decorative purposes. In addition to handling well during the manufacturing process, HX5 maintains superior performance when coated or plated whether with Cerakote, antimicrobial clearcoats, or other surface coatings like copper.
Because HX5, which is reinforced with carbon and nanofibers, can be injection molded, formed, extruded, or machined like aluminum, it can be used for complex but strong shapes. Domestically produced advanced materials are not only predictable and advantageous for supply chains, but can also be readily manufactured and mass-produced in weeks versus the months typically needed for machined metal parts.
Earlier this year, Alpine introduced billets that can be machined just like metal without the expensive outlay of creating an injection mold to significantly reduce the costs of and time needed to produce exact prototypes. The simplification of the part design process cut costs, timelines, and uncertainties, allowing more manufacturers to embrace the benefits of lightweight parts and components by using advanced materials.
About Alpine Advanced Materials
Alpine Advanced Materials is a leading expert in the design and manufacture of custom-engineered parts and products for the world’s most demanding aerospace, defense, energy, space, and outdoor applications. The company commercializes high-performance materials originally developed and qualified by top defense contractors, including its flagship HX5™ military aviation-grade thermoplastic nanocomposite.
Engineered to replace machined aluminum, HX5 is half the weight and has been both tested and proven against the harshest environments in the world. HX5 is currently in use on jet fighters, high-speed helicopters, unmanned aerial vehicles, amphibious transport vehicles, rockets, and satellites, and is highly adaptable without sacrificing strength or performance. Its customization and unrivaled manufacturability here in the U.S. combined with its high tolerance and dimensional stability make it an ideal alternative to the cost and production challenges associated with aluminum. For more information, visit www.alpineadvancedmaterials.com.